Filters
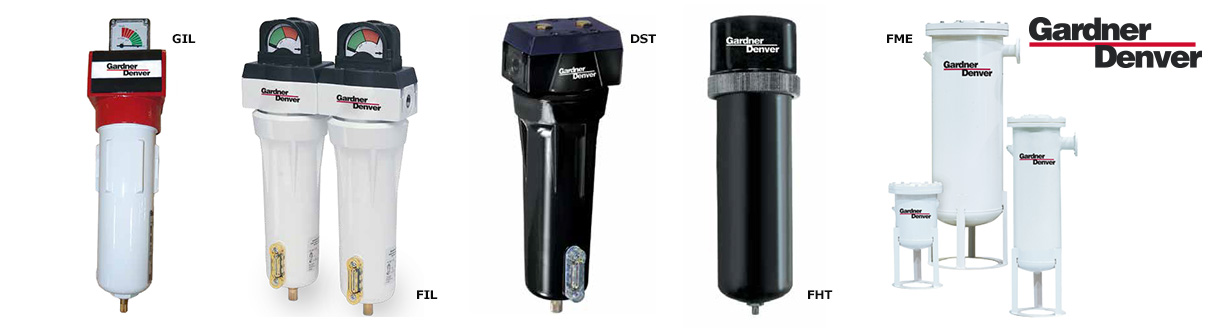
GIL Filter Series
The idea of compressed air filtration is pretty basic, identify and use media that is sure to capture the contaminants that you need to keep out of your process. Depending on the processes you perform, you may have different levels of filtration needs. The GIL Series offers a range of media sizes to help you get the level of filtration that you need. Through the GIL Series, Gardner Denver offers a comprehensive range of filter grades from High Efficiency Coalescing Filtration, Carbon Adsorption Filtration, Utility Coalescing/Particulate Filtration to Dust & Particulate Filtration.
FIL Series Filters
The FIL Series Filters provide your compressed air system with premium quality filtration for the three typical contaminant types
- Solid particles come from ambient air contaminants like dust and from rusted, oxidized pipework. They will cause pneumatic equipment to malfunction, cause instrument and control failures, and contaminate end products.
- Condensed water droplets come from the humidity in ambient air. Water will oxidize pipework and pneumatic equipment; ruin paint finishes and end products.
- Liquid oil and oil vapors are introduced by compressor lubricants and by hydrocarbon vapors present in ambient air. Oil-free compressed air is particularly important in food and pharmaceutical processes.
DST Series
How does the DST Series work? Contaminated compressed air enters the oil prefilter housing and flows from the inside of the element to the outside. Water and oil condensate falls to the bottom of the housing where it is discharged by the automatic drain. The filtered compressed air exits the filter outlet port and enters the desiccant dryer housing where the air flows downward through a bed of silica gel. At the bottom of the housing, the air flows upwards through an integrated dust filter and into an outlet air stem that takes it to the outlet port of the dryer housing.
FHT Series
Gardner Denver FHT Series filters are high temperature downstream filters designed to contain a large amount of desiccant fine microns without plugging an air system.
Operating Principle:
Phase 1 – Compressed air typically leaves a desiccant dryer containing dust concentrations up to 0.05 ppm for heatless and up to 5 ppm for heated. Particle size varies from 200 microns to about 1 micron. As the desiccant laden air enters the filter housing, a quick reduction in velocity and a sharp change of direction enables particles from 200 to 20 microns to drop out.
Phase 2 – The air then enters phase 2 where it flows through a layer of glass fabric cloth. Dust collects on the cloth becoming an efficient filter in itself. As the dust layers begin to thicken, the outer layers of dust shed off the cartridge and fall to the bottom of the housing.
Phase 3 – Reaching the 3rd and final phase, the compressed air travels through a multi-layered filter media where all remaining particles one micron and larger are captured. A final wrap of the glass fabric cloth prevents fiber migration.
FME Series – Mist Eliminators
The Gardner Denver FME Series mist eliminators are the auditor’s choice to reduce energy costs and remove oil and water aerosols from compressed air systems. The FME Series protects products and processes from contamination, increases the life of pneumatic equipment, eliminates paint appearance and adhesion problems and ultimately keeps pneumatic instruments operating.